In modern large-scale furniture manufacturing, every production step must be optimized for maximum throughput and minimal cost. Edge banding – the process of applying veneer or PVC tape to panel edges – is critical but often labor-intensive.
Installing an edgebander return conveyor is one way to automate part of the edge banding line by returning finished panels to the infeed end for further processing.
This can dramatically affect woodworking efficiency by creating a continuous, one-person operation.
However, the decision depends on factors like production volume, equipment speed, shop layout, and labor costs.
In this in-depth guide, we explore when and how a return conveyor system can improve furniture manufacturing productivity, and when it may not be cost-effective.
We draw on industry examples and technical data (including Leda Machinery’s own products) to help operations managers and production engineers make the right choice.
Featured Resource
Table of Contents
1. High-Volume Production Environments
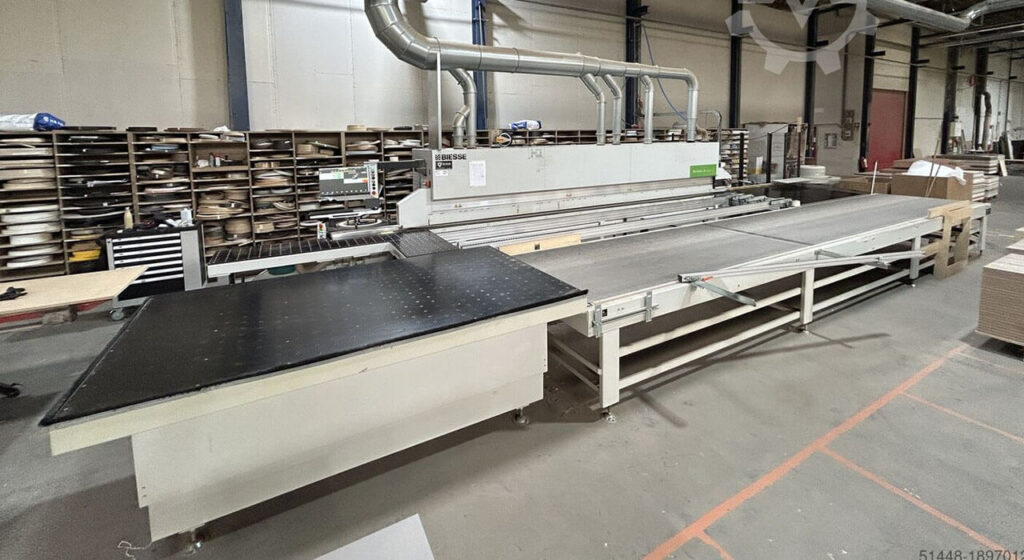
In high-speed, large-scale production settings, return conveyors often make a lot of sense.
Modern edgebanders – especially those with CNC-driven feed systems – can process long production runs of panels at speeds (often 15–23 m/min or more) that exceed what a single operator can handle manually.
Without a conveyor, one operator feeds panels into the machine while a second must remove finished pieces and stack them.
An automated return conveyor eliminates the need for a second “tail-out” operator, allowing a single skilled operator to manage the entire cycle.
This transforms edge banding into a one-person operation, effectively halving labor costs at the edgebanding station.
Key indicators that a return conveyor may be justified include:
-
Edgebander speed exceeds manual handling. If your edgebander runs at top speeds (for instance, 18 m/min) and the operator must constantly walk back and forth to retrieve parts, a conveyor lets the operator stay at the feed end, dramatically improving workflow efficiency.
Use of multiple operators for a single edgebander. If you currently need two people (one feeding, one unloading), a return conveyor can typically eliminate the need for the second person. Over time this yields significant labor savings.
-
Long, continuous runs of panels. When batching dozens or hundreds of panels in sequence, a conveyor keeps the line moving without extra handling delays. Homag notes that automated workpiece returns “optimize the entire edging process” by automating material flow, resulting in a “leaner and more efficient” workflow.
-
Integration with CNC and automated lines. Large manufacturers often have integrated production lines where panels move from saws to boring machines to edgebanders. A return conveyor fits into this automation by feeding panels back into the production flow (for example, for edge-banding multiple sides) without manual stacking. This coordinated approach maximizes overall equipment efficiency.
In practice, many high-volume cabinetry and furniture factories find that conveyors quickly pay for themselves.
For example, after installing a conveyor, one U.S. cabinet manufacturer saw virtually every edgebanding output managed by a single operator, cutting two-operator requirements in half.
Leda’s Orbit Return Conveyor and KDT Return Conveyor systems are examples of robust designs (speeds up to 13–18 m/min, modular sections, durable HPL-coated rollers, etc.) that handle high throughput.
In short, if your operation needs maximum production throughput and you have a fast edgebander capable of outpacing manual handling, a return conveyor is often a worthwhile investment.
2. Technical Features of Return Conveyor Systems
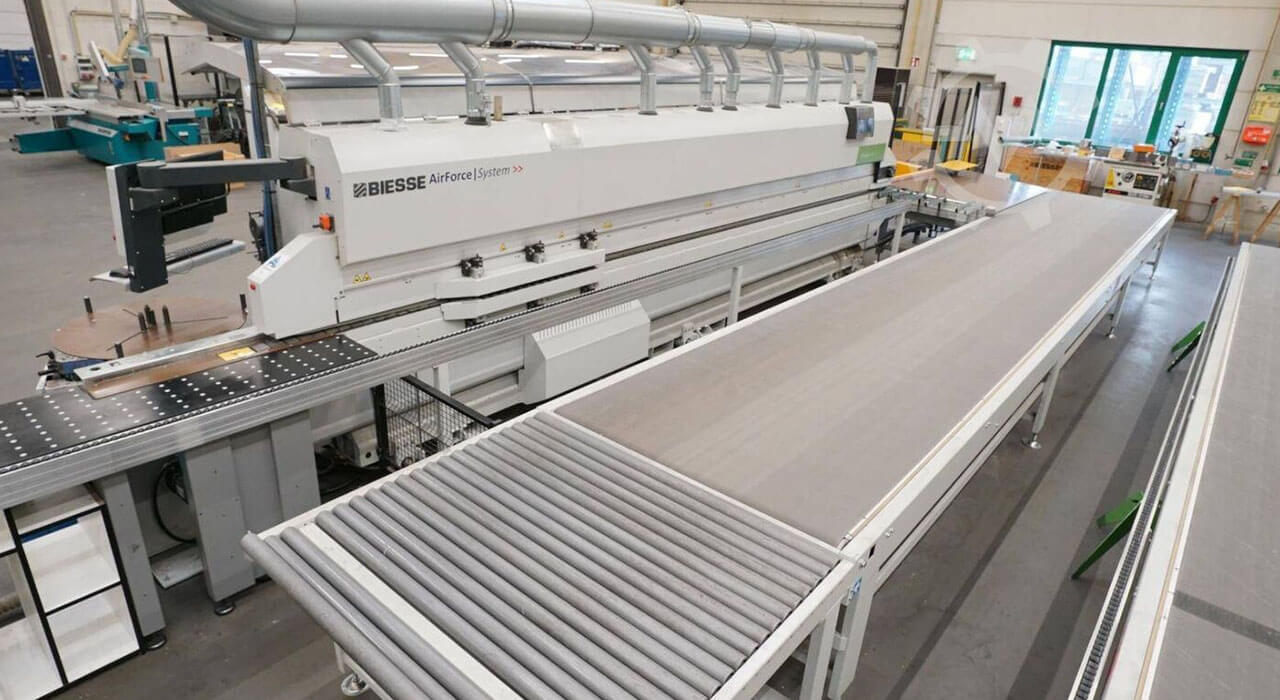
When evaluating a specific return conveyor system, it’s important to consider its technical specifications and how they match your operation:
-
Speed: Many industrial conveyors use inverter-driven variable speed controls. Leda’s Orbit model, for instance, offers up to 18 m/min, matching high-end edgebander speeds. Similarly, the KDT Return Conveyor is rated at 13–18 m/min. Ensure the conveyor speed can keep up with your fastest edgebander setting; otherwise it becomes a new bottleneck.
-
Modularity: Good return conveyors (like Leda’s Orbit) are built from modular 1000mm and 2000mm roller sections. This allows customizing the length and layout to your needs. If you ever upgrade your edgebander to a longer one, modular conveyors can be extended.
-
Construction: Heavy-duty builds ensure longevity. The Orbit conveyors feature a “combination of steel and HPL [High-Pressure Laminate]” frame and rubber-coated aluminum rollers on sealed bearings. These coated rollers help grip panels of various sizes without damage. Each module having its own drive motor (plug-and-play) means consistent traction along the line.
-
Panel Size Range: Check the minimum and maximum panel dimensions supported. For example, Leda’s Orbit system handles panels up to 2400mm in length and down to 60mm in width. If your operation uses very small parts, you may need an outfeed feeder attachment (Leda offers one) so that tiny panels can get picked up by the conveyor.
-
Feed and Eject Options: Some conveyors include cross belts or side belts to move panels laterally, or kickers to reorient parts. Accessories like a panel rotator (for changing panel orientation) or exit assist belts (for reliable pickup of small panels) are offered by manufacturers like SCM. Consider whether you need these, based on your panel sizes and shapes.
-
Maintenance and Reliability: Good conveyors have low maintenance. Orbit conveyors are advertised as “low maintenance” and “easy installation”. Look for features like quick-change belts, easy access to motors, and robust electrical components. The goal is a conveyor that can run for years in continuous production with minimal downtime.
-
Controls and Safety: Modern conveyors interface with the edgebander’s control panel or PLC. They should automatically stop if the edgebander stops (to prevent jam) and have emergency stops and guards for safety. While not always specified in product listings, check that the system meets industrial safety standards and has features like a gate switch that halts the belt if a guard is opened.
-
Integration with Equipment: Finally, ensure the conveyor is compatible with your edgebander. Leda’s return conveyors are specifically tuned for KDT edgebanders, but if you have a different brand, you may need an adapter. Key factors are matching bed height and ensuring the conveyor speed and length align with the bander’s feed rate.
In all, the technical match between conveyor and bander is crucial. A well-specified system will “simply plug in” and have one control interface. As Leda’s Orbit brochure claims, such conveyors provide “low investment and rapid payback” by virtue of smart design.
3. Return on Investment and Financial Analysis
Large-scale manufacturers naturally ask: how quickly will this pay off? Return conveyors represent a capital expense (ranging from tens to hundreds of thousands, depending on size and options), so calculating ROI is important.
A straightforward way is to compare the conveyor cost against annual labor savings.
For example, if a conveyor costs $40,000 and it eliminates one $50,000/year operator, simple payback is under one year (not counting any soft savings).
Doucet provides a detailed example: a BT3 conveyor (~$30k) pays for itself in 8 months under full production.
This assumes the removed operator cost ($50k/year) plus intangible benefits (reduced injury risk) accelerate the payoff.
Other factors in an ROI analysis include:
-
Utilization Rate: Conveyors deliver maximum benefit when the edgebander runs at high capacity continuously. If your bander only runs a few hours a day, the labor savings are lower. Doucet specifically notes that if the edgebander runs less than 2 hours per day (typical of low-volume shops), a return conveyor might not be needed.
-
Multiple Shifts: Factories that run multiple shifts (e.g. 16-24 hours) see even faster ROI since the conveyor keeps delivering savings around the clock.
-
Quality and Yield: While harder to quantify, conveyors can reduce scrap. Panels are less likely to be dropped or damaged when handled mechanically. Over time, even a small percentage of material saved can add up, boosting net output.
-
Opportunity Cost: The freed operator can be reassigned to other value-added tasks (such as assembly, finishing, maintenance), effectively multiplying productivity. If this translated into one extra technician doing other work, that’s an additional gain.
-
Equipment Depreciation and Tax: Don’t forget accounting factors. Some factories can depreciate equipment or take advantage of tax incentives for automation (depending on local rules), which improve the financial case.
While exact payback periods vary, most examples in the industry suggest under 12 months for well-used conveyors.
In contrast, a survey of smaller shops indicates that ones running the bander sporadically (part-time) typically skip conveyors entirely, relying on their one operator.
Thus, only those with sustained high volumes see a clear return on investment.
As part of the decision, managers should calculate their own break-even.
For instance: Operator annual cost × number of removed operators – Conveyor installed cost = estimated payback time. It’s prudent to include all costs (installation, potential downtime to install) and a margin for risk.
But given the labor intensiveness of edgebanding, most large operations find the math compelling.
4. When a Return Conveyor May Not Pay Off
Although return conveyors offer many benefits, they are not always justified.
In lower-volume or smaller-scale operations, the cost and space of a conveyor can outweigh its advantages. Scenarios where a conveyor might be skipped include:
-
Short, Low-Speed Edgebanders: If you have a basic bander that runs slowly (e.g. <10 m/min) and you routinely process just 2–3 panels at a time, a single operator can easily manage without delay. The extra equipment cost would not be offset by labor savings in this case.
-
Multi-Person Feeding Already: If your workflow already staggers multiple operators or has an alternate feeding scheme, a conveyor might duplicate effort.
-
Frequent Job Changes and Small Batches: If your production is dominated by custom, small-batch jobs, an operator might reuse the space for setting up the next job while running short panels. A fixed conveyor line may actually reduce flexibility for quick changeovers.
-
Limited Floor Space: As discussed, if the layout simply cannot spare the conveyor footprint without disrupting other operations, it might not be feasible.
-
Low Utilization: Factories that run the bander only occasionally (for example, doing edge banding one afternoon a week) will see minimal labor savings. In such cases, it can be cheaper to use the bands manually or invest in a smaller, low-cost conveyor (like the XPRS or BT3 Lite models mentioned by Doucet).
-
Budget Constraints: For some businesses, the capital expenditure may be reserved for other pressing needs, especially if the banding station’s inefficiency is not a top bottleneck.
The key takeaway is that the “one-size-fits-all” answer does not exist.
Leda’s own guide acknowledges this by contrasting the high-speed case (“Yes”) with the smaller operation case (“No”).
In practice, if your numbers show a multi-year payback or if the conveyor would sit idle much of the time, it might be wiser to allocate the investment elsewhere (perhaps upgrading another machine or improving process in other ways).
A careful cost-benefit analysis, including the factors above and your particular workflow, is essential.
5. Key Decision Factors for Your Operation
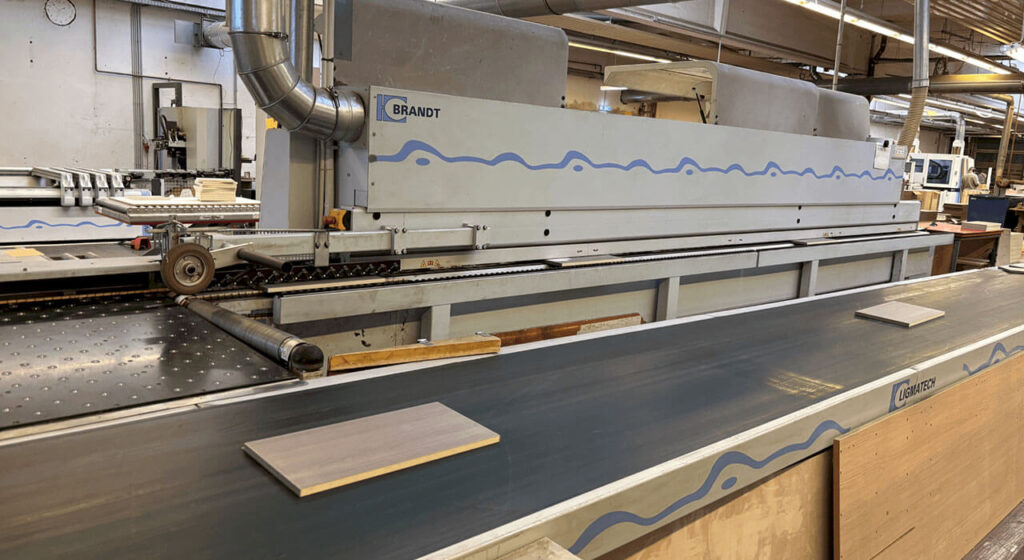
Putting it all together, here are the main factors to weigh when deciding on a return conveyor investment:
-
Production Volume and Edgebander Speed: Higher panels-per-hour throughput and faster bander speeds (e.g. >15 m/min) benefit more from conveyors. If you expect your volume to grow (future expansion), plan for automation now.
-
Labor Costs and Availability: High hourly labor costs or shortages of skilled operators make a strong case for conveyors. Calculate how many operator hours per month a conveyor would save.
-
Workshop Layout and Space: Do you have space to dedicate behind the bander? If square footage is tight or must serve multiple purposes, consider alternative outfeed solutions. If space is ample, then the conveyor’s benefits often outweigh layout concerns.
-
Equipment Compatibility: Ensure your edgebander can interface with a conveyor. (For example, KDT Edgebanders pair naturally with Leda’s conveyors.) If mixing brands, check that mounting heights and speeds can be matched.
-
Return on Investment Requirements: Set a target ROI timeline. If your financial threshold is, say, 1 year, plug in your own costs and labor savings to see if a conveyor meets it. Factor in not just salaries but also benefits and potential overtime saved.
-
Workflow Goals: Are you striving for a fully automated production line (lean, one-piece flow) or is partial automation acceptable? If the goal is maximum woodworking efficiency, conveyors align with that vision. If flexibility or manual control is more important, a conveyor might not fit your process philosophy.
-
Future-proofing: Consider if the conveyor could be reused or reconfigured if the banding machine is upgraded. Modular conveyors can adapt to different layouts or machines, adding long-term value.
By systematically evaluating these points, operations managers can make a data-driven decision.
In many cases, the combination of labor savings, increased throughput, and safer handling makes a return conveyor a compelling upgrade, especially for industrial-scale furniture factories.
6. Conclusion
An edgebander return conveyor is a powerful tool for boosting efficiency in high-volume furniture production. When matched to the right operation – one with fast equipment, high output demand, and sufficient space – it can cut labor in half and create a smooth, automated workflow.
The technology integrates seamlessly with modern CNC and robotic systems, embodying lean manufacturing principles by maintaining a continuous panel flow.
However, this investment is not universally justified.
Smaller shops or operations with low usage may find the cost and space requirements outweigh the benefits.
Ultimately, the decision hinges on your specific production profile, desired woodworking efficiency, and financial targets.
For large-scale furniture manufacturers, carefully calculating the ROI and considering future growth will guide the way.
If you determine a conveyor aligns with your goals, choosing a quality system (like Bestin’s Nova Edge Bander Return Conveyor, Leda’s KDT or Orbit conveyors) ensures reliable performance and safety.
Conversely, if flexibility and minimal footprint are more important, optimizing manual workflows or smaller conveyors could be better.
Ready to optimize your edge banding line? The experts at Bestin can advise on the right return conveyor and automation solutions for your shop’s needs.
Contact Bestin today for personalized guidance and quotes on edgebanders, return conveyors, and complete production lines tailored to maximize your furniture manufacturing productivity.