Panel saws and beam saws are two cornerstone machines for cutting large panels in woodworking.
Panel saws—available in vertical and horizontal formats—offer simplicity, affordability, and space-saving benefits, making them ideal for small shops and occasional use.
Beam saws, on the other hand, range from semi-automated to fully CNC-driven systems, delivering higher precision, faster throughput, and waste reduction, particularly for medium to high-volume operations.
Key differences include cutting mechanism (stationary blade vs moving beam), accuracy (±0.5 mm vs ±0.2 mm), productivity, shop footprint, and total cost of ownership.
This article explores definitions, types, head-to-head comparisons, buying criteria, maintenance and safety, cost-benefit analyses, and emerging automation trends to help woodworking businesses select the optimal saw for their needs.
Featured Resource
Table of Contents
1. What Are Panel Saws?
1.1. Definition and Types
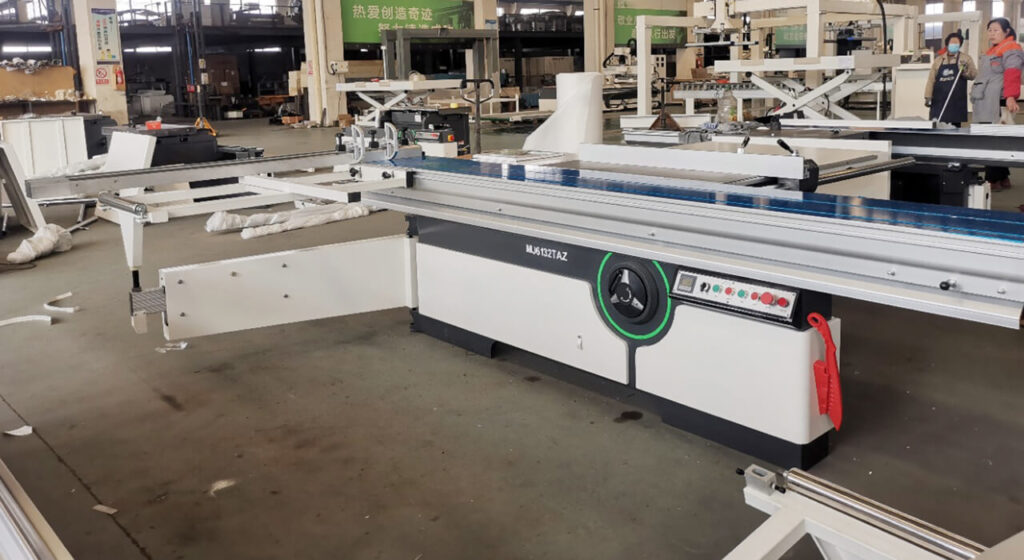
A panel saw is a woodworking machine designed to cut large sheets of wood, plywood, MDF, and similar materials into smaller panels Nesting CNC. There are two main configurations:
-
Vertical Panel Saws: Material is fed vertically against a frame while the blade moves downward. This gravity-assisted design saves shop floor space and simplifies handling of oversized panels.
-
Horizontal Panel Saws: Panels lie flat on a sliding table, and the blade or carriage moves across to execute cuts. These offer slightly higher precision but require more floor area.
1.2. Key Features
Simplicity and Cost: Panel saws feature a straightforward mechanical structure with manual or motorized operation, making them relatively inexpensive (starting around $999 for entry-level models).
-
Cutting Accuracy: Typical tolerances are around ±0.5 mm, adequate for cabinetry and light industrial use Nesting CNC.
-
Versatility: Compatible with various materials including wood, plastics, and non-ferrous metals (in specialized models).
1.3. Applications in Woodworking
Panel saws are ubiquitous in small- to mid-sized woodworking shops, furniture manufacturing, and custom cabinetry.
Their space-saving vertical models excel in compact workshops, while horizontal units deliver flat, precise cuts for high-quality furniture components.
Lower entry cost makes panel saws accessible for startups and hobbyists.
2. What Are Beam Saws?
2.1. Definition and Types
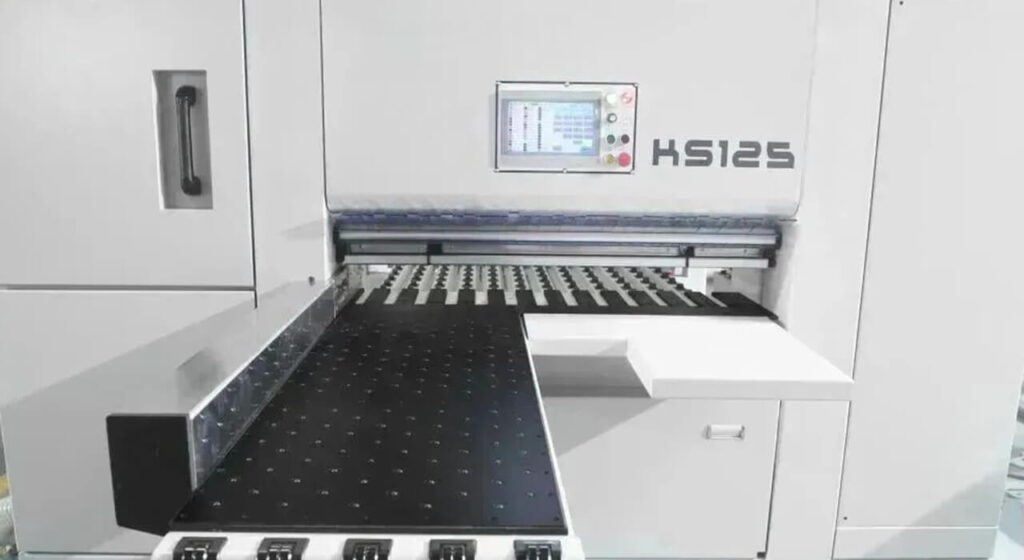
A beam saw (sometimes called a panel dividing saw) employs a moving overhead beam that carries the saw blade assembly across a stationary workpiece, enabling rapid, precise cuts of large panels. Beam saws fall into two broad categories:
- Semi-Automated Beam Saws: Operators manually load panels, then initiate programmed cut sequences. These offer improved speed and consistency over panel saws at moderate cost.
- Fully Automatic/CNC Beam Saws: Integrated feeding, offloading, and digital nesting software allow unmanned operation and optimized material yield, crucial for high-volume furniture factories.
2.2. Key Features
- High Precision: Tolerances down to ±0.2 mm or better via servo-driven axes and laser positioning systems.
- Throughput and Waste Reduction: Automated nesting routines can boost material yield by 30–40% and cut labor by up to 50% compared to sliding or panel saws.
- Flexibility: Capable of handling a variety of panel sizes, thicknesses up to 80 mm, and even non-wood substrates with appropriate tooling.
2.3. Applications in Woodworking
Panel saws are ubiquitous in small- to mid-sized woodworking shops, furniture manufacturing, and custom cabinetry.
Their space-saving vertical models excel in compact workshops, while horizontal units deliver flat, precise cuts for high-quality furniture components.
Lower entry cost makes panel saws accessible for startups and hobbyists.
3. Panel Saw vs Beam Saw: Head-to-Head Comparison
3.1. Cutting Mechanism
- Panel Saw: The blade is mounted on a fixed carriage (vertical or horizontal), and operators manually advance panels against the blade.
- Beam Saw: The blade moves on a motorized beam over a fixed panel, allowing rapid, precise, and programmable cuts without repositioning the workpiece.
3.2. Precision and Accuracy
Panel saws typically achieve ±0.5 mm accuracy, sufficient for many woodworking applications. Beam saws leverage CNC controls and laser guidance to reach ±0.2 mm or better, critical for tight-tolerance joinery and lamination.
3.3. Productivity and Throughput
Manual panel saws require operator effort for each cut, limiting daily throughput to roughly 50–100 sheets.
Semi-automated beam saws double that capacity, while fully CNC beam saws can process hundreds of panels per shift with minimal labor.
3.4. Space and Footprint
Vertical panel saws occupy as little as 1 m² of floor space. Horizontal panel saws need 4–6 m². Beam saws, due to infeed/outfeed zones and the beam mechanism, can require 10–15 m², plus clearance for material handling.
3.5. Automation and Control
Panel saws are largely manual or motor-assisted, with optional digital readouts. Beam saws offer full CNC integration, touch-screen control, barcode/GPS tracking, and networked production planning.
3.6. Cost and Return on Investment
Entry-level vertical panel saws start around $1999, while horizontal models range from $4,000 to $7,000.
Semi-automated beam saws begin at $20,000, with fully CNC systems topping $110,000.
ROI for beam saws is typically realized within 12–24 months through labor savings and reduced material waste..
4. Buying Guide: Choosing the Right Saw for Your Workshop
4.1. Assessing Your Production Needs
-
Low Volume: Occasional cuts and small runs → panel saw
-
Medium Volume: Regular production, moderate panel sizes → Horizontal panel saw
-
High Volume: Batch production, just-in-time workflows → Semi-automated or CNC beam saw
4.2. Budget Considerations
- CapEx: Initial purchase price vs financing options.
- OpEx: Power consumption, maintenance, blade replacement, software licenses.
4.3. Shop Space and Layout
Measure available floor area and ceiling height.
-
Plan material flow: loading, cutting, offloading, stacking.
4.4. Material Types and Cutting Requirements
- Thickness Range: Standard panel saws handle up to 50 mm; beam saws up to 80 mm+.
- Material Diversity: Wood, MDF, plastics, ALU-plastics → ensure compatibility of blade, fence, and dust extraction systems.
5. Technological Advancements and Trends
5.1. CNC Integration
Modern beam saws integrate with ERP/MES systems to automate job flow, track material usage, and provide real-time performance dashboards.
5.2. Automation and Digital Controls
Automated feeding/offloading units, barcode scanners, and predictive maintenance alerts reduce downtime and operator error.
5.3. Industry 4.0 Connectivity
Connected saws can send usage data to the cloud, enabling remote diagnostics, firmware updates, and analytics for continuous improvement
6. Conclusion
Choosing between a panel saw and a beam saw hinges on your shop’s production volume, budget, space constraints, and desired level of automation.
Panel saws excel in cost-sensitive, low- to medium-volume environments, offering simplicity and minimal footprint.
Beam saws justify their higher capital outlay through superior accuracy, speed, material yield, and scalability.
By aligning machine capabilities with business objectives—and adhering to best practices in maintenance and safety—woodworking operations can maximize ROI and maintain a competitive edge in an increasingly automated industry.