In the fast-paced world of furniture manufacturing, staying competitive means embracing cutting-edge solutions that boost efficiency, enhance quality, and reduce costs.
Edge banding—a vital process that applies a protective and decorative strip to the edges of furniture panels—has long relied on traditional hot melt glue methods.
While effective, these techniques come with significant drawbacks: messy application, inconsistent quality, and high energy consumption.
That’s where laser edge banding steps in as a game-changer.
This innovative technology eliminates the limitations of conventional gluing, delivering seamless, durable, and visually stunning results that elevate your production line and your products.
If you’re a woodworking professional searching for ways to optimize your operations, you’ve likely come across terms like “laser edge banding” in your research.
What does this mean for you?
It signals a completed evolution in edge band processing—one that harnesses laser precision to transform how edge bands are bonded to panels, offering unparalleled benefits over outdated methods.
In this comprehensive guide, we’ll dive deep into the world of laser edge banding, exploring its technology, processes, and real-world advantages.
By the end, you’ll see why this solution is the smart investment your business needs to thrive.
Featured Resource
Table of Contents
1. Understanding Edge Banding: The Foundation of Quality Furniture
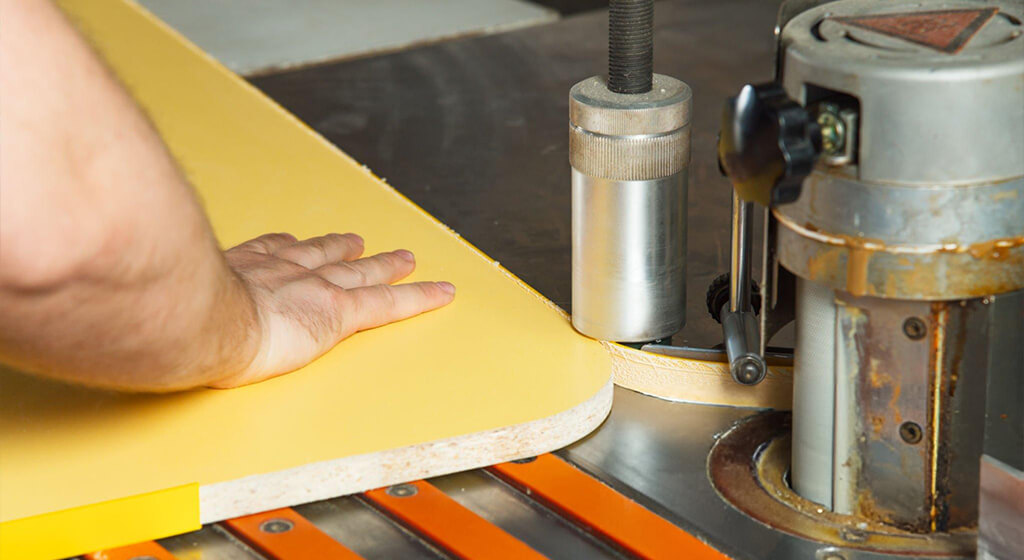
Edge banding is the unsung hero of furniture production.
It involves attaching a thin strip—typically made of plastic like PP or ABS—to the raw edges of panels such as chipboard, MDF, or honeycomb boards.
This process serves two critical purposes: it protects the panel from moisture and wear while giving the furniture a polished, professional finish.
For decades, the standard approach has been to use hot melt glues, applied with rollers in edge banding machines. The glue is heated to 150–210°C, spread onto the panel, and then the edge band is pressed into place.
But this traditional method has its flaws:
- Messy Application: Excess glue often spills over, polluting the machine and nearby components, leading to frequent cleanups and downtime.
- Energy Intensive: Keeping glue at a constant high temperature throughout the process consumes significant energy, driving up costs.
- Inconsistent Joints: The glued joint can create visible seams, detracting from the furniture’s appearance—especially on sleek, monochromatic designs. Worse, these joints are prone to water penetration, a major issue for furniture in kitchens or bathrooms.
- Chipping and Wear: Roller application can tear chips from the panel, and the bond may weaken over time, especially under heat or moisture stress.
These pain points have pushed the industry to seek better alternatives. Enter laser edge banding completed—a modern solution that redefines edge band processing for the better.
2. The Power of Laser Technology: Precision Meets Efficiency
At the heart of laser edge banding lies the remarkable science of laser technology.
A laser beam is no ordinary light—it’s coherent, meaning its waves are perfectly aligned in amplitude and phase, and monochromatic, consisting of a single wavelength.
This gives it low divergence (minimal spreading over distance) and exceptional focusability, making it ideal for precise material processing and industry, such as laser cutting machine.
In edge banding, the key to success is absorption.
When a laser beam strikes a material, its electromagnetic energy converts into thermal energy, heating the target area.
The Beer-Lambert law governs this process, showing how absorption depends on the material’s absorption coefficient and the beam’s path length.
I=I0 exp(αd)
- α=absorption coefficient
- d=path length
Unabsorbed energy is lost to reflection or transmission, but with the right setup, lasers can deliver pinpoint heat exactly where it’s needed—no mess, no waste.
For furniture manufacturers, this means a cleaner, more controlled way to bond edge bands, leaving behind the inefficiencies of hot melt glue.
But how does this technology integrate into your existing workflow? Let’s explore.
3. Integrating Laser Technology into Edge Banding Machines
Switching to laser edge banding doesn’t mean overhauling your entire setup—it’s a seamless upgrade.
In a conventional edge banding machine, the glue pot and rollers are replaced with a laser system and beam guidance components.
This eliminates the need for adhesive application in a separate gluing unit, streamlining the process from start to finish.
To accommodate various edge band widths, laser systems offer two beam guidance options:
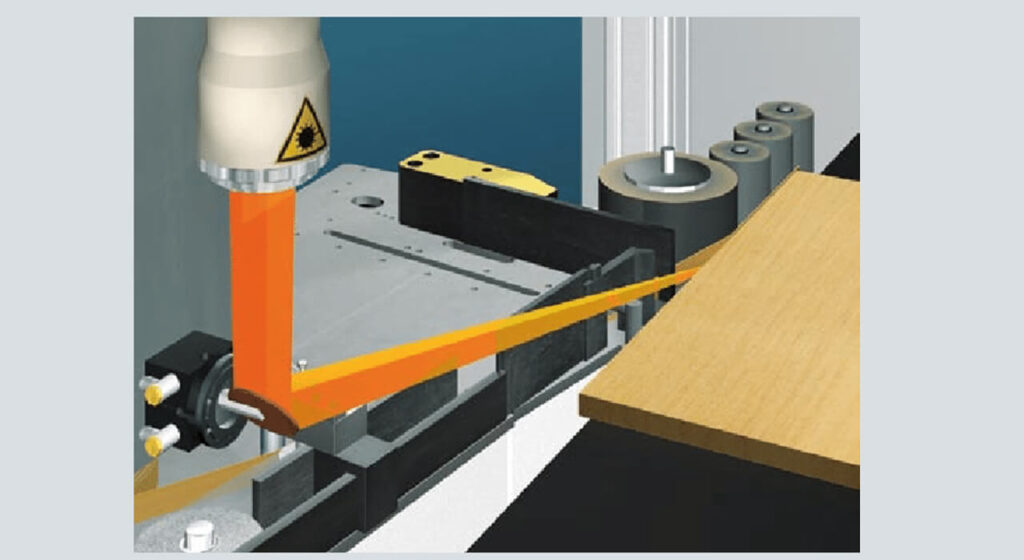
- Scanning Mirror Technology: A point-shaped laser beam is deflected into a line that spans the edge band’s width. This flexible approach adapts to different sizes instantly, making it perfect for operations with frequent changeovers.(See Above Picture)
- Beam Expander with Telescope Objectives: This method fixes the beam width, requiring less technical complexity but offering less flexibility than scanning systems.
The scanning mirror method is often preferred for its versatility, allowing you to process a wide range of materials without downtime.
By removing the glue pot, laser technology cuts maintenance, reduces energy use, and keeps your workspace cleaner—benefits that translate directly to your bottom line.
4. Material Optimization: Edge Bands Designed for Laser Precision
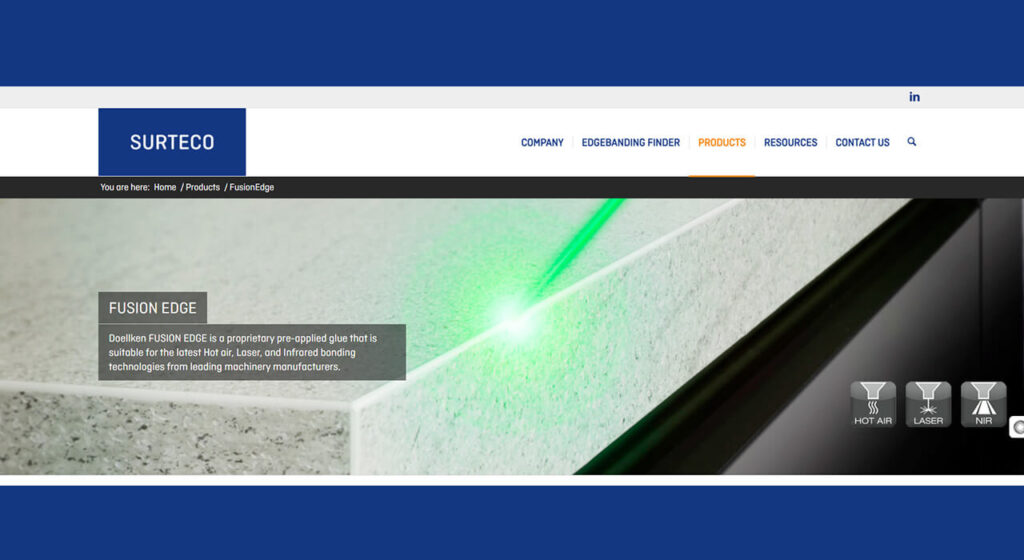
Laser edge banding isn’t just about the machine—it’s about the materials, too. Traditional edge bands relied on external glue, but laser technology demanded a smarter solution.
In collaboration with industry leaders like Döllken, manufacturers developed co-extruded edge bands tailored for laser processing. These bands feature:
- A Thermoplastic Base Layer: Made of PP or ABS, 1.0–2.0 mm thick, providing durability and flexibility.
- A Functional Layer: A thin adhesive layer replaces hot melt glue, activated by the laser’s heat.
This co-extrusion process bonds the layers together in a single step—no additional manufacturing required.
Better yet, these edge bands are compatible with traditional gluing methods, giving you the freedom to use both techniques without extra inventory costs.
The functional layer is the star of the show.
Optimized with colorants and additives, it absorbs laser energy efficiently, even in tricky materials like white, opaque, or transparent plastics that typically reflect near-infrared wavelengths (808–1064 nm).
This ensures maximum energy input, minimizing reflection risks and delivering a flawless bond every time.
5. The Laser Edge Banding Process: Step-by-Step Perfection
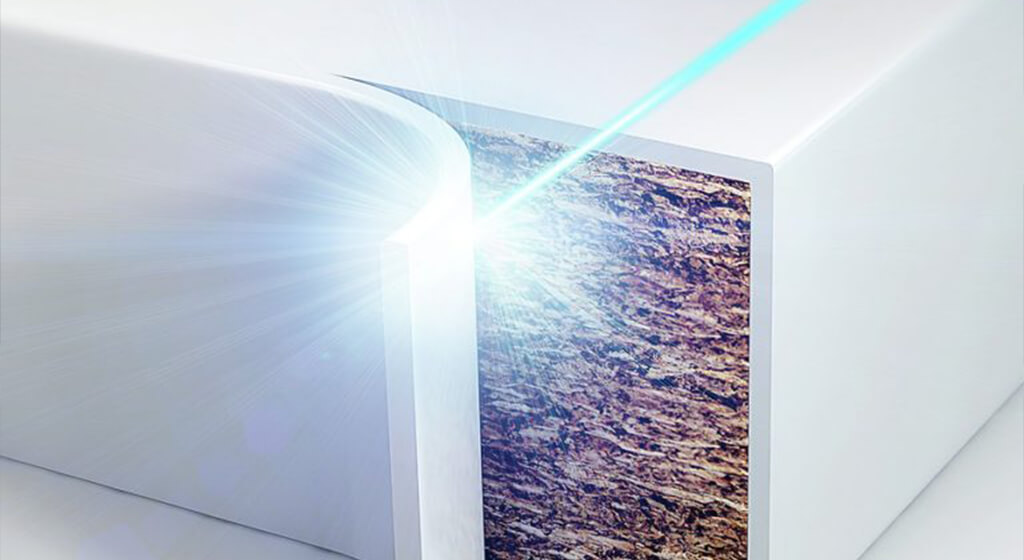
So, how does laser edge banding completed actually work? Here’s the process in action:
- Feeding the Edge Band: The co-extruded edge band is fed into the machine, just like in traditional setups.
- Laser Activation: A laser beam targets the functional layer, melting it to the perfect temperature based on parameters like power and feed rate.
- Joining the Panel: Moments after activation, the edge band meets the panel, and pressure rollers press it into place.
- Heat Dissipation: The rollers distribute the adhesive evenly into the panel’s porous surface while removing excess heat, ensuring a strong initial bond—crucial for high-speed production.
The result? A bond that’s stronger, cleaner, and ready for downstream trimming without delay.
6. Ensuring Quality with Advanced Process Control
Quality isn’t just a promise with laser edge banding—it’s a guarantee, thanks to cutting-edge process control.
Traditional gluing relied on operator skill to manage adhesive application, but laser technology brings automation and precision to the table:
- Real-Time Monitoring: Pyrometers and camera systems track temperatures in the joining zone and adjust laser power on the fly, preventing over- or under-heating.
- Post-Joining Inspection: Thermographic systems use thermal imaging to detect “cold spots” (insufficient bonding) or “hot spots” (excessive heat), ensuring every joint meets strict standards.
- Data-Driven Improvements: Temperature data before, during, and after joining provides insights for optimizing the process and documenting quality.
These tools catch defects that the naked eye might miss, like hidden adhesive failures, and allow you to remove faulty pieces early.
The result is consistent, high-quality output that builds trust with your customers.
7. The Benefits of Laser Edge Banding: Why It’s Worth the Switch
Ready to see the payoff? Laser edge banding delivers advantages that solve the pain points of traditional methods and then some:
- Superior Joint Quality: Tests (ISO 15148:2002) show laser-bonded joints absorb less water—perfect for humid environments like kitchens and bathrooms. Thermal aging tests (30 days at 60°C) confirm durability matches or exceeds conventional gluing.
- Flawless Appearance: Seamless joints eliminate visible seams, enhancing the look of monochromatic or high-end designs.
- Reduced Chipping: The laser creates a deeper, more uniform bond, minimizing edge damage during trimming or use.
- Efficiency Gains: No glue pots mean no preheating, no cleanup, and no adhesive change downtime. Switch materials in seconds, not minutes.
- Energy Savings: Lasers heat only the functional layer, not an entire glue system, cutting power consumption.
- Flexibility: Process a wider range of adhesives, including high-melt options, without compromising speed or quality.
These benefits don’t just improve your products—they streamline your operations, reduce waste, and boost profitability.
But don’t take our word for it—let’s look at the evidence.
8. Technology and Machines
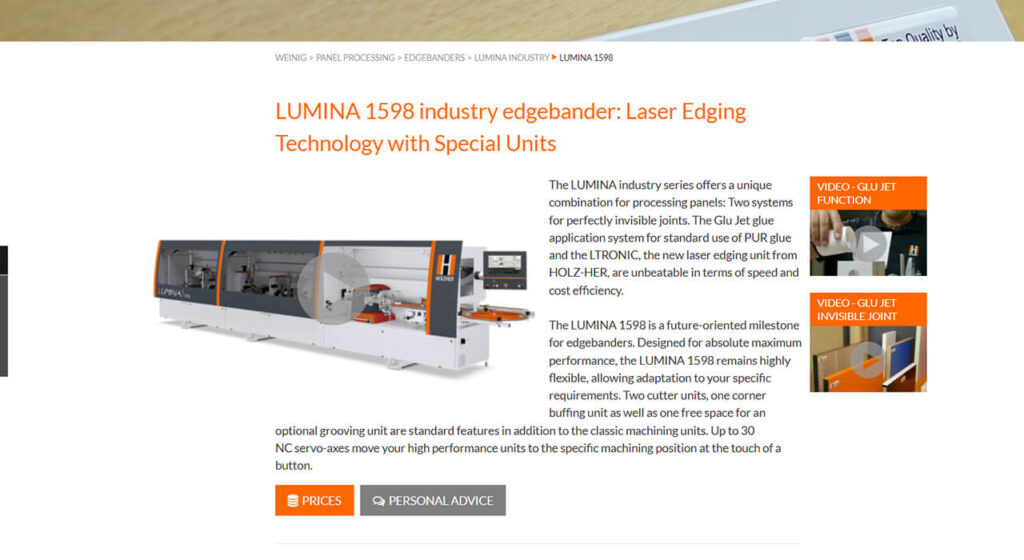
Several companies lead in laser edge banding solutions:
- REHAU LaserEdge: Uses a co-extruded polymer layer, compatible with laser, hot-air, plasma, and NIR, with a growing stock program, as per REHAU.
- Homag laserTec: Diode lasers, energy-efficient, with over 30 systems sold in Germany, from Woodworking Network.
- IMA Laser Edge Banding: Offers carbon dioxide and diode options, with flexibility for both laser and conventional gluing, noted in Woodworking Network.
- Doellken Fusion Edge: Pre-applied PUR layer activated by laser, works on straightline applications, from Woodworking Network.
These machines are designed for reliability and precision, catering to modern woodworking needs.
9. Comparison with Traditional Methods
A detailed comparison with PUR and hot-melt glue methods is essential:
Aspect | Laser Edge Banding | PUR Edge Banding |
---|---|---|
Process | Laser melts functional layer for bonding. | Uses polyurethane adhesive, activated by moisture. |
Precision and Finish | Invisible joint, seamless finish. | May leave glue line, visible on high-gloss surfaces. |
Bond Strength | Strong, resistant to heat and moisture. | High-strength but less resistant to environmental factors. |
Cost | Higher initial machine cost, long-term savings. | Lower initial cost, higher adhesive expenses. |
Production Speed | Faster, ideal for high-volume. | Efficient but slower than laser. |
Material Compatibility | Best with functional layer materials (PVC, ABS). | Works with wider range of materials. |
Environmental Impact | Less adhesive, potentially lower energy use. | Uses adhesives, higher waste from glue. |
This table, derived from Edge Band Machine, shows laser’s edge in finish and efficiency, though PUR is cheaper upfront.
10. Market Trends and Recent Developments
The laser edge banding market is poised for growth, with research suggesting expansion from 2025 to 2030, driven by demand for high-quality furniture and automation trends.
Key developments include:
- Automation and IoT Integration: Machines are increasingly equipped with IoT-enabled features for performance monitoring, aligning with Industry 4.0 trends.
- Energy Efficiency Focus: Manufacturers are developing more energy-efficient machines to address environmental concerns, though laser edge banding still uses more energy than some alternatives.
- Related Innovations: Recent developments, such as hot-air edge banding, have been available for about eight years (as of around 2020) and are gaining traction due to economic value, expected to grow exponentially. This technology offers a seamless, adhesive-free finish with benefits like better moisture and heat resistance, complementing laser edge banding’s advancements.
These trends indicate that laser edge banding remains a leader for precision and quality, particularly for premium furniture, while related technologies expand options for manufacturers.
11. Future Outlook and Industry Impact
Laser edge banding is set to become a standard in the industry, especially for high-end and moisture-resistant furniture.
Its ability to deliver flawless aesthetics, enhanced durability, and advanced process control positions it as a game-changer for woodworking professionals.
As costs potentially decrease with technological advancements and wider adoption, it may become more accessible, further driving market growth.
12. FAQ of Laser Edge Banding
What is laser edge banding?
Laser edge banding is an advanced technique that uses a high-powered laser to activate a specially designed functional layer on edge band materials, bonding them seamlessly to furniture panels without traditional adhesives.
How does laser edge banding work?
The process involves feeding a co-extruded edge band (comprising a thermoplastic base and a thin functional layer) into the machine.
A laser beam precisely heats and melts the functional layer, which then bonds to the panel surface as pressure is applied.
What are the main advantages over traditional methods?
-
Seamless Appearance: No visible glue lines or joint irregularities.
-
Improved Durability: Enhanced resistance to moisture and temperature fluctuations.
-
Process Efficiency: Faster setup and reduced maintenance since there is no need for glue pots or cleaning adhesive residue.
-
Environmental Benefits: Reduction in chemical use and VOC emissions.
What types of lasers are used in edge banding?
Which materials are compatible with laser edge banding?
Laser edge banding is most effective with co-extruded materials that have been optimized for laser processing.
Typically, these materials include thermoplastics like polypropylene (PP) or acrylonitrile butadiene styrene (ABS) with a functional layer engineered to absorb laser energy efficiently.
What is the maintenance like for laser edge banding systems?
Laser systems generally require less frequent maintenance compared to adhesive systems because there is no adhesive buildup or contamination of the application system.
However, regular calibration of sensors and routine checks on the laser’s output are essential.
13. Conclusion
Laser edge banding isn’t just an upgrade—it’s a revolution in woodworking.
It tackles the limitations of traditional methods, delivering exceptional quality, efficiency, and sustainability.
Whether you’re aiming to impress clients with flawless finishes, boost production speed, or reduce costs, this technology offers a proven solution.
Ready to take the next step? Our website features a range of cutting-edge laser edge banding machines tailored to your needs, from industrial powerhouses to versatile mid-range options.
Contact us today to explore how laser edge banding can elevate your woodworking business and keep you ahead of the competition.
Don’t settle for outdated methods—embrace the future now!